-
Table of Contents
- Exploring the Chemical Composition Differences Between A204 Gr.B and 16Mo3
- Comparing the Mechanical Properties of A204 Gr.B and 16Mo3
- Understanding the Corrosion Resistance of A204 Gr.B and 16Mo3
- Examining the Heat Treatment Requirements of A204 Gr.B and 16Mo3
- Analyzing the Weldability of A204 Gr.B and 16Mo3
- Investigating the Applications of A204 Gr.B and 16Mo3
- Comparing the Cost of A204 Gr.B and 16Mo3
- Exploring the Availability of A204 Gr.B and 16Mo3
- Conclusion
“A204 Gr.B and 16Mo3: Different Materials, Different Benefits!”
Exploring the Chemical Composition Differences Between A204 Gr.B and 16Mo3
The chemical composition of A204 Gr.B and 16Mo3 are both important when considering their use in various applications. Both materials are ferritic steels, but they differ in their chemical composition. A204 Gr.B is a low alloy steel containing molybdenum and manganese, while 16Mo3 is a chromium-molybdenum alloy steel.
A204 Gr.B contains 0.5-0.8% molybdenum and 0.5-1.0% manganese, while 16Mo3 contains 0.12-0.2% molybdenum and 0.4-0.9% chromium. The higher molybdenum content in 16Mo3 makes it more resistant to corrosion and oxidation than A204 Gr.B. Additionally, the higher chromium content in 16Mo3 gives it superior strength and hardness compared to A204 Gr.B.
The differences in chemical composition between A204 Gr.B and 16Mo3 also affect their welding characteristics. A204 Gr.B is more easily weldable than 16Mo3 due to its lower molybdenum and chromium content. However, 16Mo3 is more resistant to heat and corrosion, making it a better choice for applications that require higher temperatures or exposure to corrosive environments. depremkabinleri.com
In conclusion, A204 Gr.B and 16Mo3 are both ferritic steels, but they differ in their chemical composition. A204 Gr.B contains molybdenum and manganese, while 16Mo3 contains chromium and molybdenum. These differences affect their welding characteristics, with A204 Gr.B being more easily weldable than 16Mo3. Additionally, 16Mo3 is more resistant to heat and corrosion, making it a better choice for applications that require higher temperatures or exposure to corrosive environments.
Comparing the Mechanical Properties of A204 Gr.B and 16Mo3
The mechanical properties of A204 Gr.B and 16Mo3 are compared in this article. Both materials are ferritic steels, and they are used in a variety of applications.
A204 Gr.B is a low alloy steel that contains molybdenum and manganese. It has a yield strength of 205 MPa and a tensile strength of 380-515 MPa. It has a good weldability and is resistant to corrosion.
16Mo3 is a chromium-molybdenum steel that has a yield strength of 275 MPa and a tensile strength of 430-580 MPa. It has excellent weldability and is resistant to corrosion.
When comparing the mechanical properties of A204 Gr.B and 16Mo3, it is clear that 16Mo3 has a higher yield strength and tensile strength than A204 Gr.B. 16Mo3 also has better weldability and corrosion resistance than A204 Gr.B. Therefore, 16Mo3 is the better choice for applications that require higher strength and better weldability and corrosion resistance. depremkabinleri.com
Understanding the Corrosion Resistance of A204 Gr.B and 16Mo3
Corrosion resistance is an important factor to consider when selecting a material for a given application. A204 Gr.B and 16Mo3 are two materials that have different levels of corrosion resistance.
A204 Gr.B is a carbon-manganese steel that is commonly used in pressure vessel applications. It has good weldability and formability, and is relatively inexpensive. It has a higher carbon content than 16Mo3, which makes it more susceptible to corrosion. A204 Gr.B has a lower corrosion resistance than 16Mo3, and is not recommended for applications where corrosion resistance is a major concern.
16Mo3 is a chromium-molybdenum steel that is commonly used in high-temperature applications. It has excellent weldability and formability, and is more expensive than A204 Gr.B. 16Mo3 has a higher chromium content than A204 Gr.B, which gives it superior corrosion resistance. 16Mo3 is recommended for applications where corrosion resistance is a major concern.
In conclusion, A204 Gr.B and 16Mo3 have different levels of corrosion resistance. A204 Gr.B is less expensive and has lower corrosion resistance than 16Mo3. 16Mo3 is more expensive and has superior corrosion resistance. Therefore, it is important to consider the corrosion resistance of the material when selecting a material for a given application.
Examining the Heat Treatment Requirements of A204 Gr.B and 16Mo3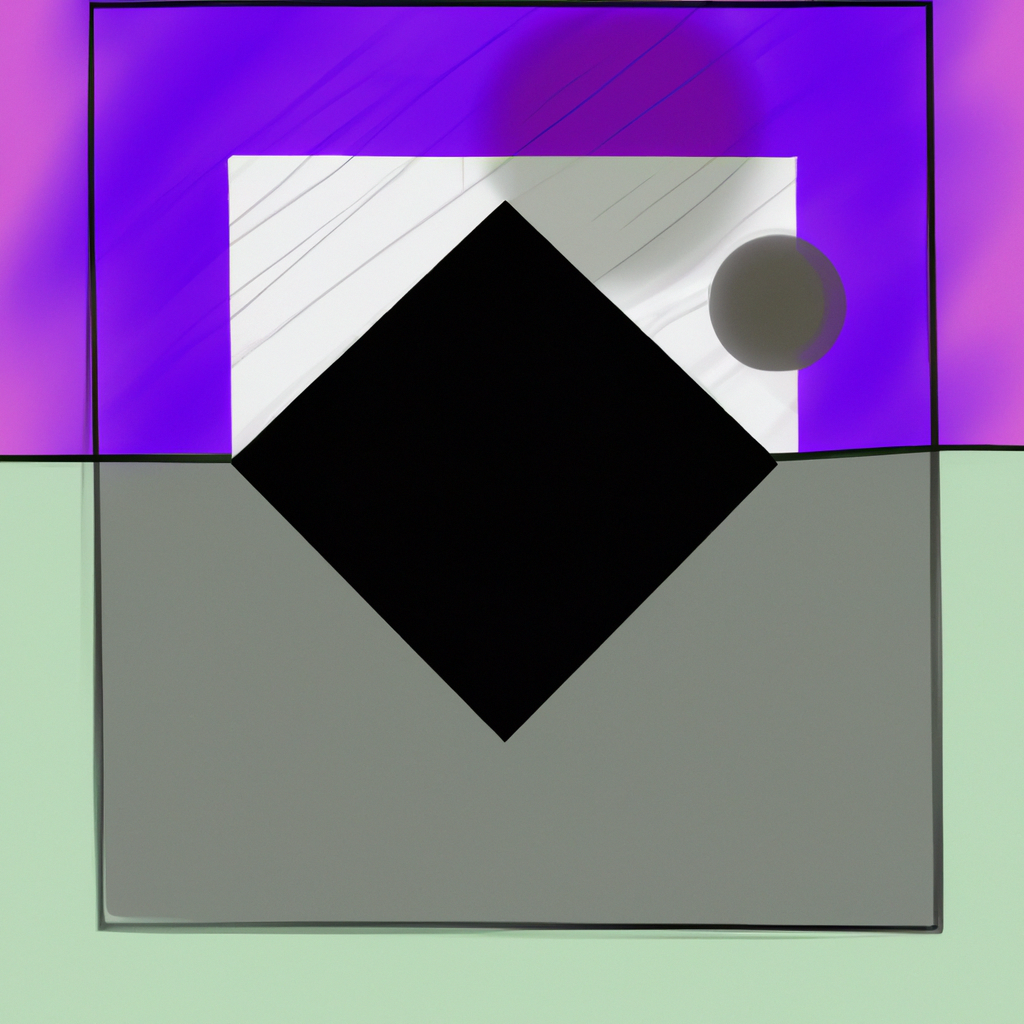
Heat treatment requirements for A204 Gr.B and 16Mo3 are important considerations when selecting these materials for use in a variety of applications. A204 Gr.B is a carbon-manganese steel alloy that is typically used in pressure vessels and boilers. 16Mo3 is a chromium-molybdenum steel alloy that is often used in high-temperature applications.
A204 Gr.B is typically supplied in the normalized and tempered condition. Normalizing involves heating the material to a temperature above the upper critical temperature and then cooling it in still air. Tempering involves reheating the material to a temperature below the lower critical temperature and then cooling it in still air. This process helps to improve the toughness and ductility of the material.
16Mo3 is typically supplied in the normalized and tempered condition as well. Normalizing involves heating the material to a temperature above the upper critical temperature and then cooling it in still air. Tempering involves reheating the material to a temperature below the lower critical temperature and then cooling it in still air. This process helps to improve the toughness and ductility of the material.
It is important to note that both A204 Gr.B and 16Mo3 should not be exposed to temperatures above their respective upper critical temperatures for extended periods of time. Doing so can lead to the formation of hard and brittle microstructures, which can reduce the material’s strength and ductility.
In conclusion, heat treatment requirements for A204 Gr.B and 16Mo3 are important considerations when selecting these materials for use in a variety of applications. Normalizing and tempering are typically used to improve the toughness and ductility of the material. It is important to note that both materials should not be exposed to temperatures above their respective upper critical temperatures for extended periods of time.
Analyzing the Weldability of A204 Gr.B and 16Mo3
Weldability is an important factor to consider when selecting a material for a given application. A204 Gr.B and 16Mo3 are two materials that are commonly used in the fabrication of welded components. In this article, we will analyze the weldability of these two materials and discuss their suitability for welding applications.
A204 Gr.B is a low alloy steel that is commonly used in the fabrication of welded components. It has good weldability and can be welded using conventional welding processes. The material is also resistant to cracking and has good corrosion resistance.
16Mo3 is a chromium-molybdenum steel that is commonly used in the fabrication of welded components. It has excellent weldability and can be welded using conventional welding processes. The material is also resistant to cracking and has good corrosion resistance.
When comparing the weldability of A204 Gr.B and 16Mo3, it is important to consider the welding process that will be used. Both materials can be welded using conventional welding processes, but 16Mo3 is more suitable for welding applications that require higher temperatures. Additionally, 16Mo3 has better corrosion resistance than A204 Gr.B, making it a better choice for applications that require corrosion resistance.
In conclusion, both A204 Gr.B and 16Mo3 are suitable for welding applications. However, 16Mo3 is more suitable for applications that require higher temperatures and better corrosion resistance. Therefore, it is important to consider the welding process and the application requirements when selecting a material for a given application.
Investigating the Applications of A204 Gr.B and 16Mo3
A204 Gr.B and 16Mo3 are two commonly used materials in the engineering and construction industries. Both materials are ferrous alloys, meaning they contain iron as their primary component. A204 Gr.B is a low alloy steel, while 16Mo3 is a chromium-molybdenum steel.
A204 Gr.B is primarily used in pressure vessels and boilers due to its excellent weldability and toughness at low temperatures. It is also used in the fabrication of industrial storage tanks and piping systems. 16Mo3 is a heat-resistant steel that is used in the fabrication of boilers, pressure vessels, and heat exchangers. It is also used in the construction of industrial furnaces and other high-temperature applications.
Both materials are highly corrosion-resistant and have excellent mechanical properties. A204 Gr.B has a yield strength of 205 MPa and a tensile strength of 380-515 MPa. 16Mo3 has a yield strength of 275 MPa and a tensile strength of 440-590 MPa. Both materials have good weldability and can be welded using conventional welding methods.
In conclusion, A204 Gr.B and 16Mo3 are two commonly used materials in the engineering and construction industries. A204 Gr.B is primarily used in pressure vessels and boilers, while 16Mo3 is used in the fabrication of boilers, pressure vessels, and heat exchangers. Both materials have excellent corrosion resistance and mechanical properties, and are highly weldable.
Comparing the Cost of A204 Gr.B and 16Mo3
When considering the cost of A204 Gr.B and 16Mo3, it is important to consider the cost of the raw materials, the cost of fabrication, and the cost of installation. A204 Gr.B is a low alloy steel that is typically used in pressure vessels and boilers. It is composed of carbon, manganese, phosphorus, sulfur, silicon, and molybdenum. 16Mo3 is a chrome-molybdenum steel alloy that is typically used in high temperature applications. It is composed of chromium, molybdenum, and manganese.
A204 Gr.B is generally less expensive than 16Mo3 due to its lower cost of raw materials. However, 16Mo3 is more expensive to fabricate due to its higher melting point and the need for additional processing steps. Additionally, 16Mo3 is more expensive to install due to its higher weight and the need for additional support structures.
Overall, A204 Gr.B is typically less expensive than 16Mo3 due to its lower cost of raw materials and fabrication. However, 16Mo3 may be more cost effective in certain applications due to its higher temperature resistance and strength.
Exploring the Availability of A204 Gr.B and 16Mo3
The availability of A204 Gr.B and 16Mo3 is dependent on the specific requirements of the application. A204 Gr.B is a chromium-molybdenum alloy steel plate intended primarily for welded boilers and pressure vessels designed for moderate and lower temperature service. It is a low alloy steel containing molybdenum and manganese as its major alloying elements. 16Mo3 is a chrome molybdenum based steel which has excellent heat resistance and corrosion resistant characteristics. It is used for a wide range of applications and is often found in the power industry and petrochemical plants.
Both A204 Gr.B and 16Mo3 are available in a variety of forms, including plates, sheets, bars, and tubes. The availability of these materials depends on the specific requirements of the application. For example, A204 Gr.B is available in thicknesses ranging from 1/4” to 4”, while 16Mo3 is available in thicknesses ranging from 1/4” to 6”. Additionally, both materials are available in a variety of grades, including A/SA204 Grade A, B, C, and D.
The availability of A204 Gr.B and 16Mo3 also depends on the specific supplier. Many suppliers offer these materials in a variety of forms and grades, and some may even offer custom fabrication services. It is important to research the specific supplier to ensure that they are able to meet the specific requirements of the application.
In conclusion, the availability of A204 Gr.B and 16Mo3 depends on the specific requirements of the application and the specific supplier. It is important to research the specific supplier to ensure that they are able to meet the specific requirements of the application.
Conclusion
In conclusion, A204 Gr.B and 16Mo3 are two different grades of steel that have different properties and applications. A204 Gr.B is a low alloy steel that is used for pressure vessels and boilers, while 16Mo3 is a high alloy steel that is used for high temperature applications. A204 Gr.B has a lower carbon content than 16Mo3, which makes it more suitable for welding and forming. 16Mo3 has a higher chromium and molybdenum content, which makes it more resistant to corrosion and oxidation. Both grades of steel have their own advantages and disadvantages, and should be chosen based on the specific application.