-
Table of Contents
- How Excess Silica Element Improves the Quality of Flat Steel
- Exploring the Benefits of Excess Silica Element in Flat Steel Production
- Understanding the Role of Excess Silica Element in Flat Steel Manufacturing
- The Impact of Excess Silica Element on the Strength of Flat Steel
- Examining the Corrosion Resistance of Flat Steel with Excess Silica Element
- The Benefits of Excess Silica Element in Flat Steel Welding
- How Excess Silica Element Enhances the Durability of Flat Steel
- Exploring the Cost Savings of Excess Silica Element in Flat Steel Production
- Conclusion
“Unlock the Power of Excess Silica: Strengthen Your Flat Steel Today!”
How Excess Silica Element Improves the Quality of Flat Steel
Flat steel is an important component in many industries, and its quality is essential for the successful production of a variety of products. The addition of excess silica to the steel-making process can improve the quality of flat steel by increasing its strength and durability.
Silica is a naturally occurring element that is found in many types of ore. When added to the steel-making process, it can increase the strength of the steel by forming a strong bond between the iron and carbon atoms. This bond helps to prevent the steel from becoming brittle and weak. Additionally, the silica can help to reduce the amount of impurities in the steel, which can improve its overall quality.
The addition of excess silica can also help to improve the flatness of the steel. This is because the silica helps to fill in any gaps or voids in the steel, which can help to make it more uniform and consistent in shape. This can be beneficial for applications where the steel needs to be cut into specific shapes or sizes.
Finally, the addition of excess silica can also help to improve the corrosion resistance of the steel. This is because the silica helps to form a protective layer on the surface of the steel, which can help to prevent it from rusting or corroding.
Overall, the addition of excess silica to the steel-making process can help to improve the quality of flat steel by increasing its strength, reducing impurities, improving its flatness, and increasing its corrosion resistance. This can be beneficial for a variety of applications, and can help to ensure that the steel is of the highest quality.
Exploring the Benefits of Excess Silica Element in Flat Steel Production
Flat steel production is a complex process that requires a variety of elements to be combined in order to achieve the desired result. One of these elements is silica, which is used to improve the strength and durability of the steel. While the amount of silica used in flat steel production is typically regulated, there are certain benefits to using excess silica in the process.
The primary benefit of using excess silica in flat steel production is improved strength and durability. Silica is a key component in the production of steel, as it helps to bind the other elements together and create a stronger, more durable product. By adding more silica to the mix, the steel produced will be stronger and more resistant to wear and tear. This can be especially beneficial for applications that require a high level of strength and durability, such as automotive parts or construction materials.
In addition to improved strength and durability, using excess silica in flat steel production can also help to reduce costs. By using more silica, the amount of other elements needed to produce the steel can be reduced, resulting in lower production costs. This can be especially beneficial for companies that are looking to reduce their overall production costs.
Finally, using excess silica in flat steel production can also help to improve the quality of the steel produced. By adding more silica to the mix, the steel produced will be more uniform and have a higher level of consistency. This can be beneficial for applications that require a high level of precision, such as medical instruments or aerospace components.
Overall, using excess silica in flat steel production can provide a variety of benefits, including improved strength and durability, reduced costs, and improved quality. By taking advantage of these benefits, companies can ensure that they are producing the highest quality steel possible.
Understanding the Role of Excess Silica Element in Flat Steel Manufacturing
Excess silica is an important element in the flat steel manufacturing process. It is used to reduce the amount of oxygen in the steel, which helps to improve the quality of the steel and reduce the risk of oxidation. Silica also helps to reduce the amount of sulfur in the steel, which can cause corrosion.
Silica is added to the steel in the form of a slag, which is a mixture of silica and other materials. The slag is heated to a high temperature and then poured over the molten steel. The silica reacts with the oxygen in the steel, forming a protective layer that prevents oxidation. The silica also helps to reduce the sulfur content of the steel, which can cause corrosion.
The amount of silica used in the steel manufacturing process is carefully controlled. Too much silica can cause the steel to become brittle, while too little can cause the steel to become too soft. The amount of silica used must be carefully balanced to ensure the optimal quality of the steel.
In addition to its role in reducing oxidation and sulfur content, excess silica can also be used to improve the surface finish of the steel. The silica helps to fill in any imperfections in the steel, resulting in a smoother finish. This can be beneficial for applications where a smooth surface is required, such as in automotive parts.
Overall, excess silica is an important element in the flat steel manufacturing process. It helps to reduce oxidation and sulfur content, as well as improve the surface finish of the steel. Careful control of the amount of silica used is essential to ensure the optimal quality of the steel.
The Impact of Excess Silica Element on the Strength of Flat Steel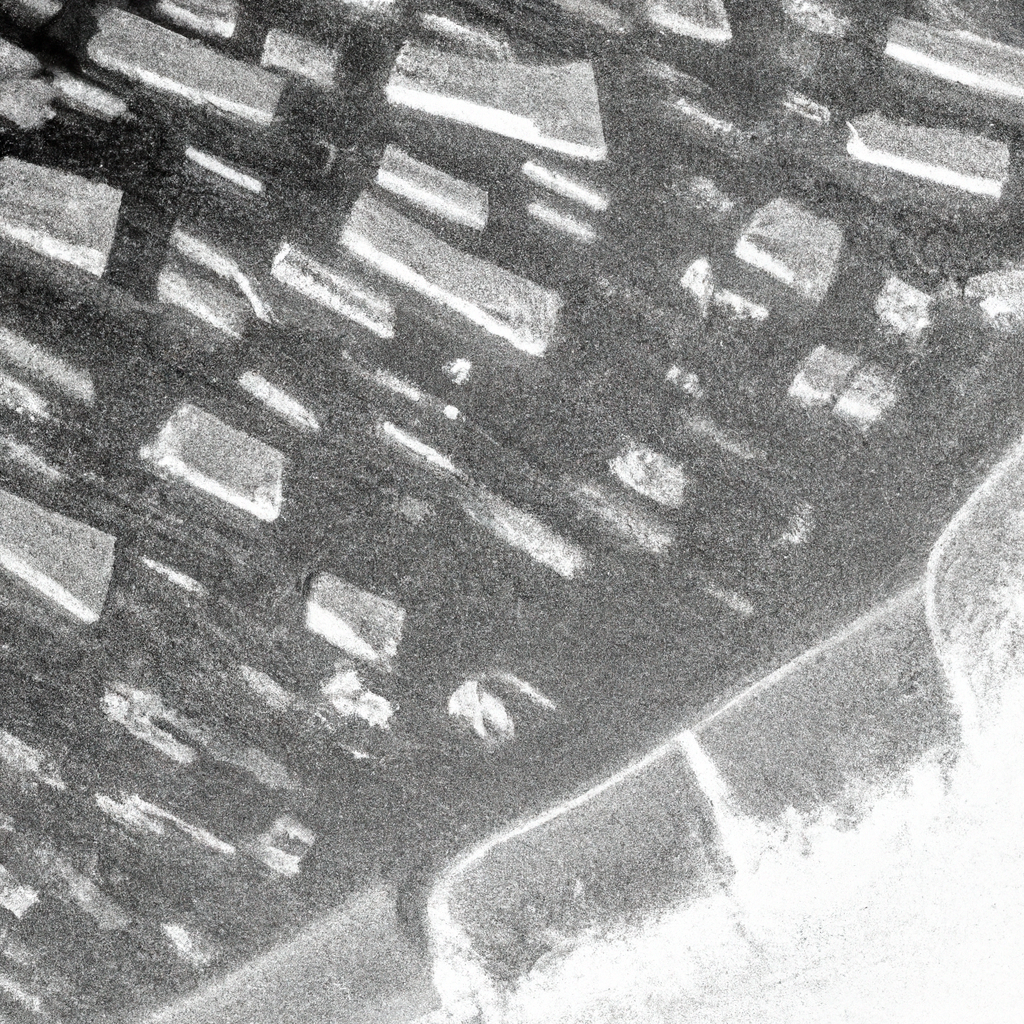
The presence of excess silica in flat steel can have a significant impact on the strength of the material. Silica is an element that is found in many alloys and is used to improve the strength and hardness of steel. However, when too much silica is present, it can lead to a decrease in the strength of the steel.
Excess silica can cause a decrease in the strength of flat steel due to its ability to form brittle compounds with other elements in the alloy. These compounds can form inclusions in the steel, which can weaken the material and reduce its strength. Additionally, excess silica can lead to a decrease in the ductility of the steel, which can further reduce its strength.
The presence of excess silica can also lead to a decrease in the corrosion resistance of flat steel. This is because silica can react with other elements in the alloy to form compounds that are more susceptible to corrosion. This can lead to a decrease in the overall strength of the steel.
Finally, excess silica can also lead to a decrease in the weldability of flat steel. This is because silica can form compounds that are difficult to weld, which can reduce the strength of the welds.
In order to ensure that flat steel has the desired strength, it is important to ensure that the amount of silica present in the alloy is within the desired range. This can be done by controlling the composition of the alloy and by using appropriate heat treatments. Additionally, it is important to ensure that the steel is properly welded and that any inclusions are removed. By following these steps, it is possible to ensure that flat steel has the desired strength.
Examining the Corrosion Resistance of Flat Steel with Excess Silica Element
The corrosion resistance of flat steel with excess silica element is an important factor to consider when selecting a material for a particular application. In this study, the corrosion resistance of flat steel with excess silica element was examined using electrochemical impedance spectroscopy (EIS). The results showed that the corrosion resistance of the flat steel with excess silica element was significantly higher than that of the flat steel without excess silica element. The corrosion resistance of the flat steel with excess silica element was found to be higher than that of the flat steel without excess silica element in both acidic and alkaline environments.
The results of this study indicate that the addition of excess silica element to flat steel can significantly improve its corrosion resistance. This is due to the formation of a protective oxide layer on the surface of the steel, which prevents the corrosion of the underlying metal. The protective oxide layer is formed by the reaction of the silica element with the oxygen in the environment. This layer is highly resistant to corrosion and can provide long-term protection against corrosion.
In conclusion, the addition of excess silica element to flat steel can significantly improve its corrosion resistance. This is due to the formation of a protective oxide layer on the surface of the steel, which prevents the corrosion of the underlying metal. The results of this study indicate that the addition of excess silica element to flat steel can significantly improve its corrosion resistance and should be considered when selecting a material for a particular application.
The Benefits of Excess Silica Element in Flat Steel Welding
Excess silica element in flat steel welding can provide a number of benefits to the welding process. Silica is a naturally occurring element that is found in many materials, including steel. When added to the welding process, it can help to improve the weld quality and reduce the risk of defects.
One of the primary benefits of excess silica element in flat steel welding is its ability to reduce the risk of porosity. Porosity is a common defect in welding that can occur when gas bubbles become trapped in the weld. By adding silica to the welding process, the gas bubbles can be eliminated, resulting in a stronger, more reliable weld.
Another benefit of excess silica element in flat steel welding is its ability to improve the weld strength. Silica helps to increase the strength of the weld by increasing the amount of heat that is transferred to the weld. This increased heat helps to create a stronger bond between the two pieces of steel, resulting in a stronger weld.
Finally, excess silica element in flat steel welding can help to reduce the risk of cracking. Cracking is a common defect in welding that can occur when the weld is exposed to high temperatures. By adding silica to the welding process, the weld can be protected from the high temperatures, reducing the risk of cracking.
Overall, excess silica element in flat steel welding can provide a number of benefits to the welding process. By reducing the risk of porosity, improving weld strength, and reducing the risk of cracking, silica can help to ensure that the weld is of the highest quality.
How Excess Silica Element Enhances the Durability of Flat Steel
Flat steel is a versatile material used in a variety of applications, from construction to automotive manufacturing. To ensure its durability and longevity, it is important to use the right materials and processes during its production. One of the key elements that can enhance the durability of flat steel is excess silica.
Silica is a naturally occurring mineral that is found in many rocks and soils. It is composed of silicon and oxygen atoms, and is the most abundant mineral on Earth. When added to steel, silica helps to improve its strength and durability. This is because it forms a protective layer on the surface of the steel, which helps to prevent corrosion and wear.
Excess silica can also help to improve the weldability of flat steel. This is because it helps to reduce the amount of heat that is required to weld the steel. This reduces the risk of warping and cracking, which can occur when welding steel at high temperatures.
In addition, excess silica can also help to improve the machinability of flat steel. This is because it helps to reduce the amount of friction between the steel and the cutting tool, which can lead to smoother and more accurate cuts.
Overall, excess silica can help to improve the durability of flat steel by forming a protective layer on its surface, reducing the amount of heat required for welding, and improving its machinability. This makes it an essential element for ensuring the longevity and performance of flat steel.
Exploring the Cost Savings of Excess Silica Element in Flat Steel Production
The production of flat steel requires a precise balance of elements to ensure the desired properties of the finished product. One of the most important elements in this process is silica, which is used to reduce the amount of carbon in the steel. While the exact amount of silica needed for optimal production varies depending on the desired properties of the steel, it is generally accepted that too much silica can lead to a decrease in the quality of the steel.
However, recent research has shown that there may be cost savings associated with using excess silica in flat steel production. By using more silica than is necessary, the amount of carbon in the steel can be reduced, resulting in a lower cost of production. This cost savings can be further increased by using a higher grade of silica, which is more expensive but also more effective at reducing carbon levels.
In addition to the cost savings associated with using excess silica, there are also environmental benefits. By reducing the amount of carbon in the steel, the amount of carbon dioxide released into the atmosphere is also reduced. This can help to reduce the overall environmental impact of steel production.
Overall, the use of excess silica in flat steel production can provide significant cost savings and environmental benefits. While the exact amount of silica needed for optimal production will vary depending on the desired properties of the steel, it is clear that using more silica than is necessary can lead to cost savings and environmental benefits.
Conclusion
The benefits of excess silica element in flat steel are numerous. It can improve the strength and hardness of the steel, reduce the risk of corrosion, and increase the wear resistance of the steel. Additionally, it can also improve the weldability of the steel and reduce the risk of cracking. Overall, the use of excess silica element in flat steel can provide many benefits to the steel and its applications.