-
Table of Contents
- What Are the Benefits of Zinc Coil Sheet Coatings?
- How to Choose the Right Zinc Coil Sheet Coating for Your Project
- Unlock the Secret to Creating Shinier, Durable Zinc Coil Sheet Coatings
- The Pros and Cons of Different Zinc Coil Sheet Coating Techniques
- How to Properly Prepare a Surface for Zinc Coil Sheet Coating
- The Latest Innovations in Zinc Coil Sheet Coating Technology
- How to Maintain and Repair Zinc Coil Sheet Coatings
- Common Mistakes to Avoid When Applying Zinc Coil Sheet Coatings
- Conclusion
“Unlock the Power of Zinc: Shine Bright and Last Longer with Coil Sheet Coatings!”
What Are the Benefits of Zinc Coil Sheet Coatings?
Zinc Coil Sheet Coatings offer a range of benefits for a variety of applications. Zinc is a highly corrosion-resistant metal, making it an ideal choice for protecting steel and other metals from rust and corrosion. Zinc coatings are also highly durable, providing long-term protection against wear and tear. Additionally, zinc coatings are relatively inexpensive and easy to apply, making them a cost-effective solution for many applications.
Zinc coatings are also aesthetically pleasing, providing a bright, shiny finish that can enhance the appearance of a product. Zinc coatings are also non-toxic and environmentally friendly, making them a safe choice for many applications. Finally, zinc coatings are highly resistant to UV radiation, making them an ideal choice for outdoor applications.
Overall, zinc coil sheet coatings offer a range of benefits for a variety of applications. They are highly corrosion-resistant, durable, cost-effective, aesthetically pleasing, non-toxic, and UV resistant. As such, they are an ideal choice for many applications.
How to Choose the Right Zinc Coil Sheet Coating for Your Project
When selecting a zinc coil sheet coating for a project, it is important to consider the environment in which the coating will be used. Different coatings are designed to provide different levels of protection against corrosion, abrasion, and other environmental factors.
The first step in choosing the right zinc coil sheet coating is to determine the environment in which the coating will be used. Different coatings are designed to provide different levels of protection against corrosion, abrasion, and other environmental factors. For example, a coating designed for use in a marine environment will need to be more resistant to saltwater corrosion than a coating designed for use in a dry environment.
The next step is to consider the type of coating that is best suited for the project. Zinc-rich coatings are the most common type of zinc coil sheet coating and are available in a variety of formulations. These coatings are designed to provide a high level of protection against corrosion and abrasion. Zinc-rich coatings are also available in a variety of colors, allowing for a wide range of aesthetic options.
In addition to zinc-rich coatings, there are also other types of coatings available. These include epoxy-based coatings, which are designed to provide a high level of protection against corrosion and abrasion, as well as a variety of other environmental factors. Epoxy-based coatings are also available in a variety of colors, allowing for a wide range of aesthetic options.
Finally, it is important to consider the cost of the coating. Zinc-rich coatings are typically more expensive than other types of coatings, but they provide a higher level of protection against corrosion and abrasion. Epoxy-based coatings are typically less expensive, but they may not provide the same level of protection.
By considering the environment in which the coating will be used, the type of coating that is best suited for the project, and the cost of the coating, it is possible to choose the right zinc coil sheet coating for a project. With the right coating, projects can be completed with confidence, knowing that the coating will provide the necessary protection against corrosion and abrasion.
Unlock the Secret to Creating Shinier, Durable Zinc Coil Sheet Coatings
Zinc coil sheet coatings are an important part of many industrial and commercial applications. They provide a durable, corrosion-resistant finish that can withstand harsh environmental conditions. To ensure the highest quality and longest-lasting finish, it is important to understand the key elements of creating a successful zinc coil sheet coating.
The first step in creating a successful zinc coil sheet coating is to ensure that the substrate is properly prepared. This includes cleaning the surface of any dirt, grease, or other contaminants, as well as removing any existing coatings. Once the substrate is clean and dry, it should be treated with a suitable primer to ensure proper adhesion of the zinc coating.
The next step is to apply the zinc coating. This can be done using a variety of methods, including hot-dip galvanizing, electroplating, or spray-on coatings. Each method has its own advantages and disadvantages, so it is important to select the best method for the application.
Once the zinc coating has been applied, it is important to ensure that it is properly cured. This can be done by baking the coated substrate in an oven at a temperature of around 400°F for a period of time. This will ensure that the zinc coating is fully cured and will provide a durable, corrosion-resistant finish.
Finally, it is important to ensure that the zinc coating is properly sealed. This can be done by applying a clear topcoat or sealant to the zinc coating. This will help to protect the zinc coating from environmental elements and will also help to create a shinier, more durable finish.
By following these steps, you can ensure that your zinc coil sheet coatings will provide a durable, corrosion-resistant finish that will last for years to come.
The Pros and Cons of Different Zinc Coil Sheet Coating Techniques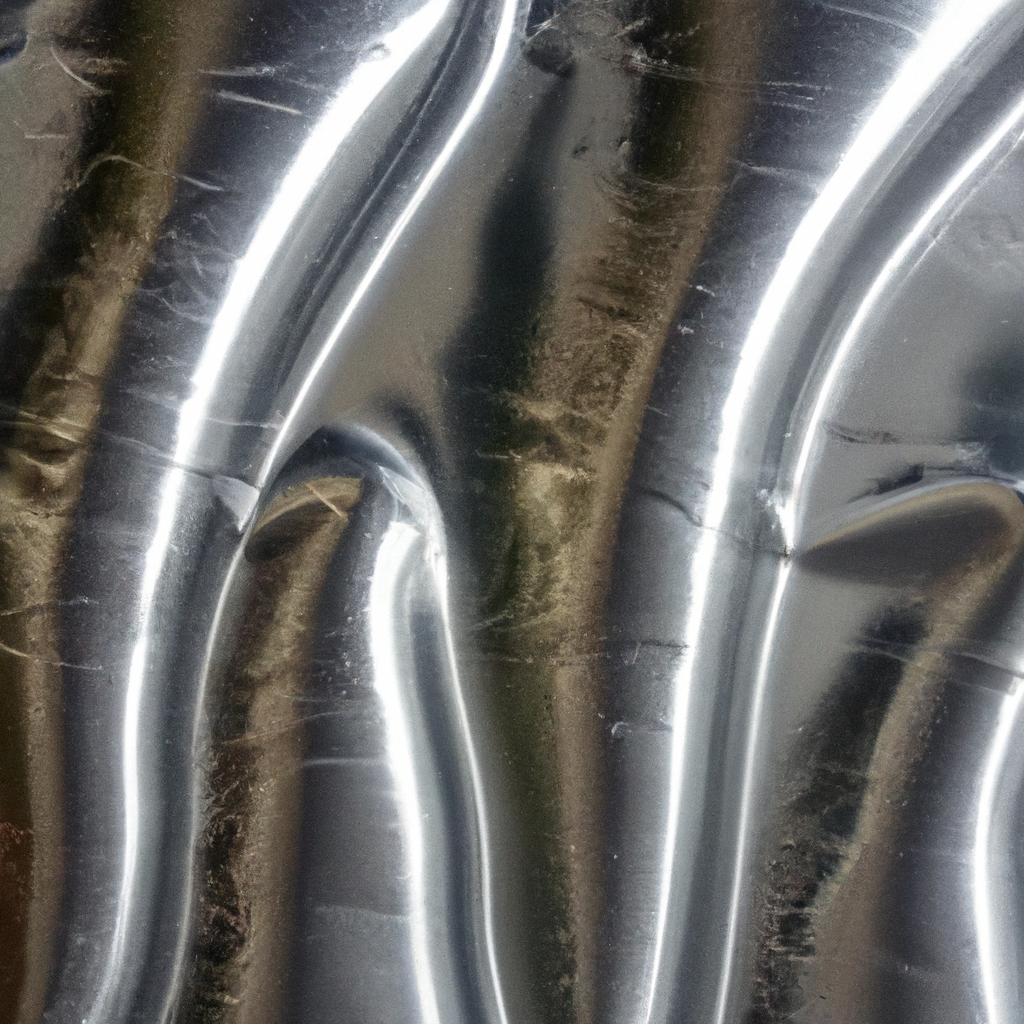
Zinc coil sheet coating is a popular method of protecting metal surfaces from corrosion. It is used in a variety of industries, including automotive, construction, and marine. The process involves applying a thin layer of zinc to the surface of the metal, which acts as a barrier against corrosion. There are several different techniques for applying zinc coil sheet coating, each with its own advantages and disadvantages.
Hot-Dip Galvanizing: Hot-dip galvanizing is the most common method of zinc coil sheet coating. It involves dipping the metal into a bath of molten zinc, which forms a protective layer on the surface. The main advantage of this technique is that it provides a very durable coating that is resistant to corrosion and wear. The main disadvantage is that it is a time-consuming process and can be expensive.
Electroplating: Electroplating is another popular method of zinc coil sheet coating. It involves applying a thin layer of zinc to the surface of the metal using an electric current. The main advantage of this technique is that it is relatively quick and inexpensive. The main disadvantage is that the coating is not as durable as hot-dip galvanizing and may not provide adequate protection against corrosion.
Spray Coating: Spray coating is a relatively new technique for zinc coil sheet coating. It involves spraying a thin layer of zinc onto the surface of the metal. The main advantage of this technique is that it is fast and relatively inexpensive. The main disadvantage is that the coating is not as durable as hot-dip galvanizing and may not provide adequate protection against corrosion.
These are just a few of the different techniques for zinc coil sheet coating. Each has its own advantages and disadvantages, so it is important to consider all of them before deciding which one is best for your application.
How to Properly Prepare a Surface for Zinc Coil Sheet Coating
Surface preparation is an essential step in the zinc coil sheet coating process. Proper preparation of the surface ensures that the coating adheres properly and provides the desired protection. The following steps should be taken to properly prepare a surface for zinc coil sheet coating:
1. Clean the surface: The surface should be thoroughly cleaned to remove any dirt, dust, grease, oil, or other contaminants. A degreaser or solvent cleaner can be used to remove any oils or greases. A pressure washer can be used to remove dirt and dust.
2. Remove any rust: Any rust on the surface should be removed using a wire brush or sandpaper.
3. Sand the surface: The surface should be sanded with a medium-grit sandpaper to create a smooth, uniform surface.
4. Clean the surface again: After sanding, the surface should be cleaned again to remove any dust or debris.
5. Prime the surface: A primer should be applied to the surface to ensure proper adhesion of the zinc coil sheet coating.
Following these steps will ensure that the surface is properly prepared for zinc coil sheet coating and will provide the desired protection.
The Latest Innovations in Zinc Coil Sheet Coating Technology
The use of zinc coil sheet coating technology has been a popular choice for many industries due to its durability and corrosion resistance. As technology advances, so does the development of new and improved zinc coil sheet coating technologies. Here, we will discuss the latest innovations in zinc coil sheet coating technology.
One of the most recent developments in zinc coil sheet coating technology is the use of zinc-aluminum alloy coatings. This type of coating is a combination of zinc and aluminum, which provides superior corrosion resistance and improved durability. The alloy coating also offers improved adhesion to the substrate, making it ideal for use in a variety of applications.
Another recent development in zinc coil sheet coating technology is the use of zinc-nickel alloy coatings. This type of coating is a combination of zinc and nickel, which provides superior corrosion resistance and improved durability. The alloy coating also offers improved adhesion to the substrate, making it ideal for use in a variety of applications.
The use of zinc-titanium alloy coatings is another recent development in zinc coil sheet coating technology. This type of coating is a combination of zinc and titanium, which provides superior corrosion resistance and improved durability. The alloy coating also offers improved adhesion to the substrate, making it ideal for use in a variety of applications.
Finally, the use of zinc-magnesium alloy coatings is another recent development in zinc coil sheet coating technology. This type of coating is a combination of zinc and magnesium, which provides superior corrosion resistance and improved durability. The alloy coating also offers improved adhesion to the substrate, making it ideal for use in a variety of applications.
These are just a few of the latest innovations in zinc coil sheet coating technology. As technology continues to advance, more advancements in this field are sure to come. It is important to stay up to date on the latest developments in order to ensure that your products are using the most advanced and reliable coating technologies available.
How to Maintain and Repair Zinc Coil Sheet Coatings
Zinc coil sheet coatings are a popular choice for many industrial applications due to their corrosion resistance and durability. However, like any other coating, zinc coil sheet coatings require regular maintenance and repair to ensure they remain in good condition. Here are some tips for maintaining and repairing zinc coil sheet coatings:
1. Clean the surface regularly. Dirt and debris can accumulate on the surface of the zinc coil sheet coating, which can lead to corrosion and other damage. Regularly cleaning the surface with a mild detergent and water can help prevent this.
2. Inspect the coating regularly. Regularly inspecting the coating can help identify any areas that may need repair. Look for signs of corrosion, cracking, or peeling.
3. Repair any damage promptly. If any damage is found, it should be repaired as soon as possible to prevent further damage. This can be done by sanding down the affected area and applying a new layer of zinc coating.
4. Apply a protective coating. Applying a protective coating such as a clear sealant or wax can help protect the zinc coil sheet coating from further damage.
5. Store the zinc coil sheet coating properly. When not in use, the zinc coil sheet coating should be stored in a cool, dry place. This will help prevent corrosion and other damage.
By following these tips, you can help ensure that your zinc coil sheet coating remains in good condition for years to come.
Common Mistakes to Avoid When Applying Zinc Coil Sheet Coatings
1. Not Cleaning the Surface Properly: Before applying a zinc coil sheet coating, it is essential to ensure that the surface is clean and free of any dirt, dust, or debris. If the surface is not properly cleaned, the coating may not adhere properly and could lead to premature failure.
2. Not Pre-Treating the Surface: Pre-treating the surface with a suitable primer or etching solution is essential for ensuring that the zinc coil sheet coating adheres properly. Not pre-treating the surface can lead to poor adhesion and premature failure.
3. Not Applying the Coating Evenly: It is important to ensure that the zinc coil sheet coating is applied evenly and in a uniform manner. If the coating is applied unevenly, it can lead to premature failure and poor adhesion.
4. Not Applying the Coating Thick Enough: It is important to ensure that the zinc coil sheet coating is applied thick enough to provide adequate protection. If the coating is too thin, it may not provide adequate protection and could lead to premature failure.
5. Not Allowing the Coating to Cure Properly: After the zinc coil sheet coating has been applied, it is important to allow it to cure properly. If the coating is not allowed to cure properly, it may not adhere properly and could lead to premature failure.
Conclusion
In conclusion, Unlock the Secret to Creating Shinier, Durable Zinc Coil Sheet Coatings is an invaluable resource for anyone looking to improve the quality and durability of their zinc coil sheet coatings. By following the steps outlined in this guide, you can create a superior product that will last longer and look better than ever before. With the right knowledge and materials, you can unlock the secret to creating shinier, durable zinc coil sheet coatings.