-
Table of Contents
- The Benefits of Carbon in Steel Production: How Carbon Improves the Quality of Steel
- The Role of Carbon in Steel Production: How Carbon Enhances the Strength of Steel
- The Impact of Carbon on Steel Production: How Carbon Affects the Cost of Steel
- The History of Carbon in Steel Production: How Carbon Has Been Used for Centuries
- The Future of Carbon in Steel Production: How Carbon Will Continue to Play a Role in Steel Production
- The Challenges of Carbon in Steel Production: How Carbon Can Be Difficult to Control
- The Regulations of Carbon in Steel Production: How Carbon Is Regulated to Ensure Quality Steel
- The Righteousness of Carbon in Steel Production: How Carbon Is Essential for Quality Steel
- Conclusion
“The Righteousness of Carbon: Steel Production at its Finest!”
The Benefits of Carbon in Steel Production: How Carbon Improves the Quality of Steel
Carbon is an essential element in the production of steel. It is the primary alloying element that provides the desired properties in the final product. Carbon is added to steel in order to increase its strength, hardness, and wear resistance. It also improves the steel’s ability to resist corrosion and oxidation.
The addition of carbon to steel increases its strength and hardness by forming a hard, wear-resistant surface layer. This layer is known as martensite, and it is formed when the carbon atoms bond with the iron atoms in the steel. The martensite layer is very hard and resistant to wear, making it ideal for applications that require a durable material.
The addition of carbon also improves the steel’s ability to resist corrosion and oxidation. Carbon atoms form a protective layer on the surface of the steel, which prevents oxygen and other corrosive elements from attacking the metal. This layer also helps to reduce the rate of oxidation, which can cause the steel to weaken over time.
Finally, the addition of carbon to steel improves its machinability. Carbon atoms form a lubricating layer on the surface of the steel, which reduces friction and makes it easier to machine. This makes it easier to produce complex shapes and parts with precision.
In summary, the addition of carbon to steel improves its strength, hardness, wear resistance, corrosion resistance, and machinability. These properties make it an ideal material for a wide range of applications, from automotive components to construction materials. Carbon is an essential element in the production of steel, and its addition can significantly improve the quality of the final product.
The Role of Carbon in Steel Production: How Carbon Enhances the Strength of Steel
Carbon is an essential element in the production of steel, as it enhances the strength of the material. Steel is an alloy of iron and carbon, and the amount of carbon present in the alloy determines the properties of the steel. The higher the carbon content, the stronger the steel.
When carbon is added to molten iron, it forms a series of compounds known as iron carbides. These compounds are harder and stronger than the iron itself, and they form a matrix that strengthens the steel. The higher the carbon content, the more iron carbides are formed, and the stronger the steel becomes.
In addition to increasing the strength of steel, carbon also increases its hardness. This is because the iron carbides formed by the carbon are harder than the iron itself. The higher the carbon content, the harder the steel becomes.
Carbon also increases the wear resistance of steel. This is because the iron carbides formed by the carbon are more resistant to wear than the iron itself. The higher the carbon content, the more wear-resistant the steel becomes.
Finally, carbon increases the ductility of steel. This is because the iron carbides formed by the carbon are more ductile than the iron itself. The higher the carbon content, the more ductile the steel becomes.
In summary, carbon is an essential element in the production of steel, as it enhances the strength, hardness, wear resistance, and ductility of the material. The higher the carbon content, the stronger, harder, more wear-resistant, and more ductile the steel becomes.
The Impact of Carbon on Steel Production: How Carbon Affects the Cost of Steel
Carbon is a key component in the production of steel, and its impact on the cost of steel production is significant. Carbon is added to steel during the production process in order to increase its strength and hardness. The amount of carbon added to steel affects the cost of production, as the higher the carbon content, the more expensive the steel will be.
The cost of steel production is largely determined by the amount of carbon added to the steel. The higher the carbon content, the more expensive the steel will be. This is because the higher the carbon content, the more energy is required to produce the steel. The higher the energy requirement, the higher the cost of production.
The cost of steel production is also affected by the type of carbon used. Different types of carbon have different properties, and the type of carbon used will affect the cost of production. For example, high-carbon steel is more expensive to produce than low-carbon steel, as it requires more energy to produce.
The cost of steel production is also affected by the quality of the carbon used. High-quality carbon is more expensive than low-quality carbon, as it requires more energy to produce. The higher the quality of the carbon, the higher the cost of production.
In conclusion, carbon is a key component in the production of steel, and its impact on the cost of steel production is significant. The amount of carbon added to steel affects the cost of production, as the higher the carbon content, the more expensive the steel will be. The type and quality of carbon used also affects the cost of production, as high-carbon steel and high-quality carbon are more expensive to produce than low-carbon steel and low-quality carbon.
The History of Carbon in Steel Production: How Carbon Has Been Used for Centuries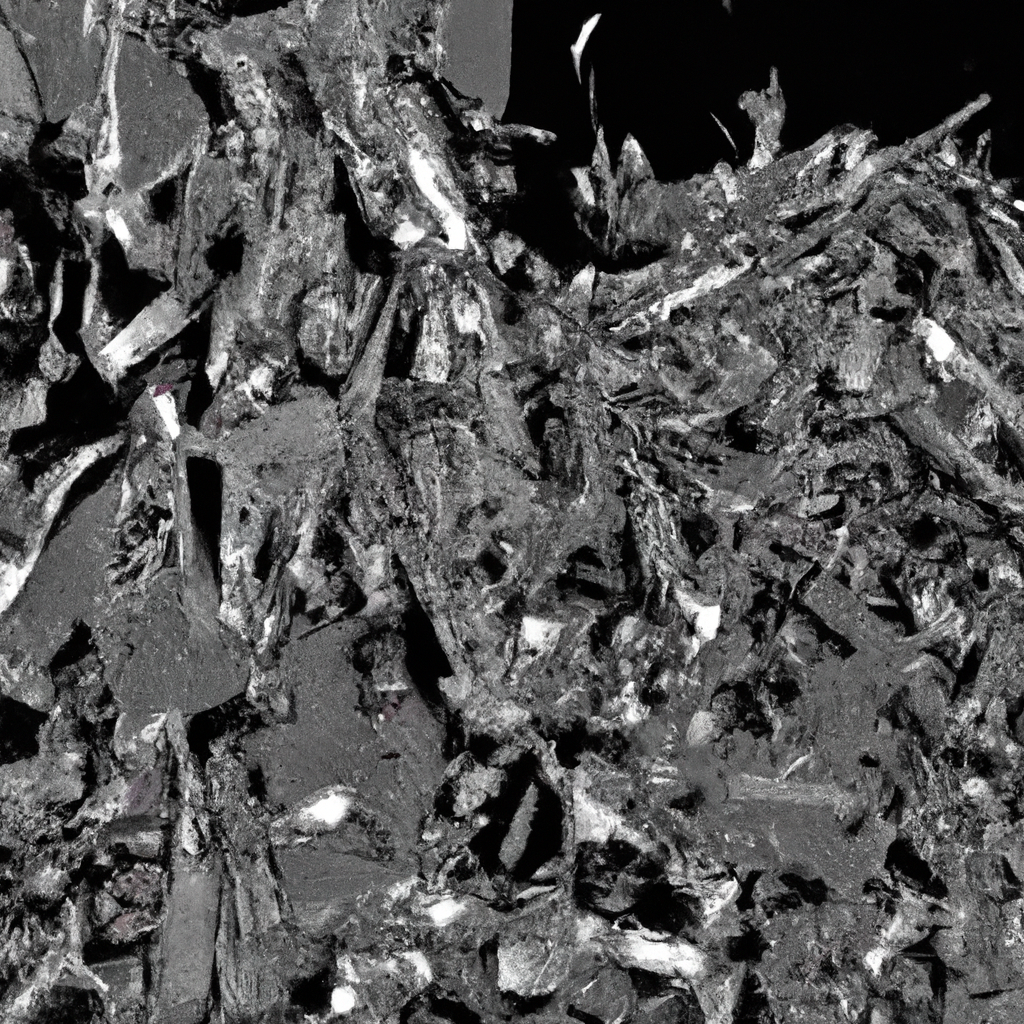
Carbon has been used in steel production for centuries, and its importance in the process has only grown over time. Carbon is a key element in the production of steel, as it is responsible for the strength and hardness of the metal. The use of Carbon in Steel Production dates back to the early 1800s, when it was first used to produce cast iron.
At the time, carbon was added to molten iron in order to reduce its melting point and increase its strength. This process, known as carburization, allowed for the production of cast iron with a higher carbon content than was previously possible. This allowed for the production of steel with greater strength and hardness than ever before.
In the late 1800s, the Bessemer process was developed, which allowed for the mass production of steel. This process involved the use of oxygen to burn off impurities in molten iron, and the addition of carbon to increase the strength and hardness of the steel. This process allowed for the production of steel with a higher carbon content than was previously possible.
In the early 1900s, the open-hearth process was developed, which allowed for the production of steel with an even higher carbon content. This process involved the use of a furnace to heat the molten iron and the addition of carbon to increase the strength and hardness of the steel. This process allowed for the production of steel with an even higher carbon content than was previously possible.
Today, carbon is still an important element in steel production. It is used to increase the strength and hardness of the steel, as well as to improve its corrosion resistance. Carbon is also used to reduce the cost of steel production, as it is a relatively inexpensive element.
The use of carbon in steel production has been essential for centuries, and its importance in the process has only grown over time. Carbon is a key element in the production of steel, as it is responsible for the strength and hardness of the metal. Its use has allowed for the production of steel with higher carbon content than was previously possible, and its cost-effectiveness has made it an essential element in steel production.
The Future of Carbon in Steel Production: How Carbon Will Continue to Play a Role in Steel Production
Carbon has been a key component in steel production for centuries, and its importance is unlikely to diminish in the future. As the world continues to move towards a more sustainable future, the steel industry is looking for ways to reduce its carbon footprint while still producing high-quality steel. To this end, the industry is exploring a variety of methods to reduce the amount of carbon used in steel production.
One of the most promising methods is the use of alternative fuels such as natural gas, hydrogen, and biomass. These fuels can be used to replace coal and coke, which are the primary sources of carbon in steel production. Natural gas and hydrogen are both clean-burning fuels that produce fewer emissions than coal and coke, and biomass can be used to produce a carbon-neutral fuel. By replacing coal and coke with these alternative fuels, steel producers can reduce their carbon emissions while still producing high-quality steel.
Another way to reduce the amount of carbon used in steel production is through the use of advanced technologies such as electric arc furnaces and direct reduced iron (DRI). Electric arc furnaces use electricity to heat the steel, which reduces the amount of carbon needed to produce the steel. DRI is a process that uses natural gas to reduce iron ore into iron without the need for coal or coke. By using these technologies, steel producers can reduce their carbon emissions while still producing high-quality steel.
Finally, steel producers are also exploring the use of carbon capture and storage (CCS) technologies. CCS technologies capture carbon dioxide from the steel production process and store it underground, preventing it from entering the atmosphere. This technology is still in its early stages, but it has the potential to significantly reduce the amount of carbon used in steel production.
In conclusion, carbon will continue to play an important role in steel production in the future. Steel producers are exploring a variety of methods to reduce their carbon emissions while still producing high-quality steel. These methods include the use of alternative fuels, advanced technologies, and carbon capture and storage technologies. By utilizing these methods, steel producers can reduce their carbon emissions while still producing high-quality steel.
The Challenges of Carbon in Steel Production: How Carbon Can Be Difficult to Control
Carbon is a key element in steel production, as it is responsible for the strength and hardness of the steel. However, controlling the amount of carbon in the steel can be a challenge. Too much carbon can lead to brittleness and cracking, while too little can lead to a softer, weaker steel.
The amount of carbon in steel is determined by the composition of the raw materials used in the production process. The carbon content of the raw materials must be carefully monitored to ensure that the desired amount of carbon is present in the steel. This can be difficult, as the carbon content of the raw materials can vary significantly depending on the source.
In addition, the carbon content of the steel can be affected by the temperature of the furnace used in the production process. If the temperature is too high, the carbon content of the steel will increase, while if the temperature is too low, the carbon content will decrease. This makes it difficult to maintain a consistent carbon content in the steel.
Finally, the carbon content of the steel can be affected by the amount of time it spends in the furnace. If the steel is left in the furnace for too long, the carbon content will increase, while if it is removed too soon, the carbon content will decrease. This makes it difficult to control the carbon content of the steel.
In summary, controlling the amount of carbon in steel production can be a challenge. The carbon content of the raw materials must be carefully monitored, and the temperature and duration of the furnace must be carefully controlled to ensure that the desired amount of carbon is present in the steel. By taking these steps, steel producers can ensure that the steel they produce has the desired strength and hardness.
The Regulations of Carbon in Steel Production: How Carbon Is Regulated to Ensure Quality Steel
The regulation of carbon in steel production is essential to ensure the quality of the final product. Carbon is a key element in the production of steel, as it is responsible for the strength and hardness of the material. As such, it is important to ensure that the correct amount of carbon is present in the steel.
The regulation of carbon in steel production is achieved through a combination of processes. Firstly, the raw materials used in the production of steel must be carefully selected to ensure that the correct amount of carbon is present. This is typically done by analyzing the chemical composition of the raw materials and adjusting the proportions accordingly.
Once the raw materials have been selected, the steel must be heated to a specific temperature in order to achieve the desired carbon content. This is typically done in a furnace, where the temperature can be precisely controlled. The temperature must be carefully monitored throughout the process to ensure that the correct amount of carbon is present in the steel.
Finally, the steel must be cooled in order to achieve the desired properties. This is typically done by quenching the steel in water or oil. The cooling process must be carefully monitored to ensure that the correct amount of carbon is present in the steel.
By carefully regulating the amount of carbon present in the steel, it is possible to ensure that the final product meets the desired quality standards. This is essential for producing high-quality steel that is suitable for a variety of applications.
The Righteousness of Carbon in Steel Production: How Carbon Is Essential for Quality Steel
Carbon is an essential element in the production of quality steel. It is the primary alloying element that gives steel its strength and hardness. Carbon is also responsible for the steel’s ability to be heat treated, which is essential for a variety of applications. Without carbon, steel would be too soft and brittle to be of any use.
The amount of carbon in steel is measured in percentages, with the most common range being between 0.2% and 2.1%. The higher the percentage of carbon, the harder and stronger the steel will be. However, too much carbon can make the steel brittle and difficult to work with. Therefore, it is important to find the right balance of carbon in order to produce quality steel.
The most common way to add carbon to steel is through the use of a carbon-rich material such as coke or charcoal. This material is heated to a high temperature and then mixed with the molten steel. The carbon then diffuses into the steel, forming a homogenous mixture.
The carbon content of steel can also be adjusted through the use of various heat treatments. These treatments can be used to increase or decrease the amount of carbon in the steel. For example, a process known as carburizing can be used to increase the carbon content of steel. This process involves heating the steel in a carbon-rich atmosphere, which causes the carbon to diffuse into the steel.
In conclusion, carbon is an essential element in the production of quality steel. It is responsible for the steel’s strength and hardness, as well as its ability to be heat treated. The amount of carbon in steel must be carefully controlled in order to achieve the desired properties. Carbon can be added to steel through the use of carbon-rich materials or through various heat treatments. Without carbon, steel would be too soft and brittle to be of any use.
Conclusion
The Righteousness of Carbon in Steel Production is an important factor in the production of steel. Carbon is a key component in the production of steel, and its presence is essential for the production of high-quality steel. Carbon is also a major contributor to the environmental impact of steel production, and its use must be carefully managed to ensure that it is used responsibly. By understanding the importance of carbon in steel production, and by taking steps to reduce its environmental impact, steel producers can ensure that their products are produced in a way that is both responsible and sustainable.