Production of steel from iron ore
Ore containing iron
The iron sprouts that were taken from the ground were analyzed, and the ones that had the most iron were listed below.
> Magnetic > Hematite > Limonite > siderite > Pyrite
Magnesite is a kind of mineral that has a naturally occurring magnetic field. Even though it has the greatest iron concentration, it is not favored because of its level of iron. The reason for this is because it has the potential to induce faults in the blast furnace that are very difficult to fix.
Hematite: The subsurface is often composed of stone, sand, dirt, and other similar materials. It may be discovered in conjunction with other drugs. Its concentration in the sprout might range anywhere from 40 to 60 percent of the total. This sprout is responsible for 9 percent of the world’s total iron output despite the fact that it does not possess any magnetic properties.
Next to hematite, the most common usage for the iron ore limonite is in the production of steel. This material is a kind of iron ore that contains 30–50% iron. The most common kind of limonite ore has 30–50% iron in its composition.
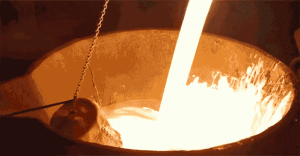
Casium (Ca) and manganese are often found in close proximity to siderite, which is the mineral known as siderite (Mg). As a consequence, there is a relatively low iron rate. While siderite is necessary for the production of iron, it is not necessary to add limestone to the blast furnace since there is already sufficient limestone present in the sprout.
Pyrite is a kind of iron ore that also contains sulfur in its composition. This sprout, on the other hand, is not recommended due to the presence of sulfur. In the event that it is put to use, the sulfur will need to be burnt in a separate process. Because sulfur makes iron more brittle, iron is more susceptible to breaking.
Raw iron may be obtained by the use of a blast furnace.
Iron (raw iron), as well as iron sprouts, may be produced in melting furnaces that use blast furnaces. The height of the blast furnace ranges anywhere from 30 to 90 meters, and its diameter at its widest point, which is in the shape of a truncated cone, is between 8 and 10 meters.
The exterior half of the groove is covered with steel sheeting, while the inside of the furnace is lined with chamotte, also known as fire brick, that has a thickness of 1.5 meters and is able to sustain very high temperatures.
As soon as the blast furnace is ignited, it will continue to burn without stopping for the next ten to fifteen years, or until it breaks down. The temperature within the main chamber of the furnace will remain constant going forward. The area around the furnace is continually cooled with water in order to avoid the high temperature from causing any harm to the body of the furnace itself.
It seems that the mixture has been filled. At the very top of the furnace is where all of the gases that are produced during the combustion process but do not catch fire: carbon gas and the other gases.
This gas is often referred to as mouth gas or gas from the blast furnace. The air that is introduced into the blast furnace is heated by the gas that is produced by the blast furnace.
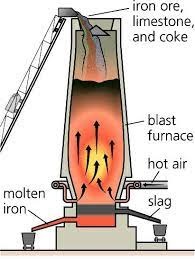
The term “Reduction Zone” refers to the zone of the iron ore processing plant where potentially dangerous chemicals are heated (decomposed and discharged as gas).
In this area, it eliminates the oxygen present in the sprout by independently accumulating carbon.
To put it another way, the carbon absorbs the oxygen that is present in the iron that is located in the inner area and then releases it as carbon monoxide (CO).
FeO+C→Fe + CO or CO +C→2CO
The process of decomposing iron from other materials by melting it in a blast furnace is known as reduction.
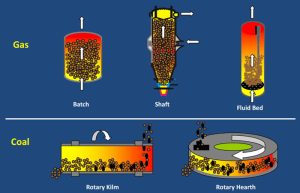
The drying zone is located in the top portion of the blast furnace. This portion requires temperatures between 300 and 360 degrees Celsius and then dries out. It is a combination of iron ore, coke lime, and limestone.
The reduction (oxidation) or reduction zone makes up the second section of the furnace.
In this area, the oxide that is present in the iron ore begins to break down. This occurrence is chemical in nature.
First zone drying zone
Second drying zone zone
The process of removing carbon from the iron takes place in the third zone of the furnace. This zone has a straight reduction between 900 and 1100 degrees Celsius.
Reduction is the process of removing iron from non-iron materials by melting while making a lot of noise.
The third zone (900-1100 degrees Celsius)
During this period in which these chemical processes are taking place, the decomposed (reduced) iron begins to melt and flow into the chamber.
Raw iron is the name given to the first product that may be produced from iron ore (pig).
The strong impact of raw iron requires three to five percent carbon. Raw iron may also be processed into steel and other steel products.