-
Table of Contents
- What Is High Carbon Steel and How Is It Used in Welding?
- What Are the Benefits of Welding High Carbon Steel?
- What Are the Different Types of High Carbon Steel?
- What Are the Safety Precautions for Welding High Carbon Steel?
- What Are the Different Techniques for Welding High Carbon Steel?
- What Are the Best Practices for Welding High Carbon Steel?
- What Are the Common Challenges of Welding High Carbon Steel?
- What Are the Different Types of Welding Rods for High Carbon Steel?
- Conclusion
“Weld high carbon steel with Confidence – Get the Job Done Right!”
What Is High Carbon Steel and How Is It Used in Welding?
High carbon steel is a type of steel that contains a higher amount of carbon than other types of steel. It is typically used in the production of tools and machinery, and is also used in welding.
High carbon steel is known for its strength and durability, making it an ideal material for welding. It is often used in applications that require high strength and wear resistance, such as in the construction of bridges and buildings. It is also used in the production of knives, swords, and other cutting tools.
When welding high carbon steel, it is important to use the correct welding technique. This is because high carbon steel is more prone to cracking and warping than other types of steel. It is also important to use the correct welding rod and filler metal. The welding rod should be made of a material that is compatible with the high carbon steel, such as a low-hydrogen rod. The filler metal should also be compatible with the high carbon steel, such as a nickel-based filler metal.
When welding high carbon steel, it is important to use the correct welding parameters. This includes the welding current, voltage, and travel speed. It is also important to use the correct shielding gas, such as an argon-based gas.
High carbon steel is a versatile material that can be used in a variety of welding applications. It is important to use the correct welding technique and parameters to ensure a successful weld.
What Are the Benefits of Welding High Carbon Steel?
Welding high carbon steel offers a number of benefits, including increased strength, improved wear resistance, and greater ductility. High carbon steel is a type of steel that contains a higher amount of carbon than other types of steel, making it more difficult to weld. However, with the right welding techniques, high carbon steel can be welded successfully.
The increased strength of high carbon steel makes it an ideal choice for applications that require a strong, durable material. The higher carbon content also makes it more resistant to wear and tear, making it a great choice for parts that will be exposed to high levels of stress or friction. Additionally, the increased ductility of high carbon steel makes it easier to shape and form into complex shapes.
Overall, welding high carbon steel offers a number of benefits, including increased strength, improved wear resistance, and greater ductility. With the right welding techniques, high carbon steel can be welded successfully, making it an ideal choice for a variety of applications.
What Are the Different Types of High Carbon Steel?
High carbon steel is a type of steel that contains a higher amount of carbon than other types of steel. It is typically used in applications that require strength and durability, such as blades, springs, and cutting tools. There are several different types of high carbon steel, each with its own unique properties and uses.
The most common type of high carbon steel is 1095 steel. This type of steel is often used in knives and swords due to its high strength and hardness. It is also used in springs and other applications that require a high level of strength and durability.
Another type of high carbon steel is 52100 steel. This type of steel is often used in bearings and other applications that require a high level of wear resistance. It is also used in some cutting tools due to its high hardness and wear resistance.
A third type of high carbon steel is O1 steel. This type of steel is often used in chisels and other cutting tools due to its high hardness and wear resistance. It is also used in some springs due to its high strength and durability.
Finally, there is D2 steel. This type of steel is often used in punches and dies due to its high wear resistance and hardness. It is also used in some cutting tools due to its high strength and durability.
What Are the Safety Precautions for Welding High Carbon Steel?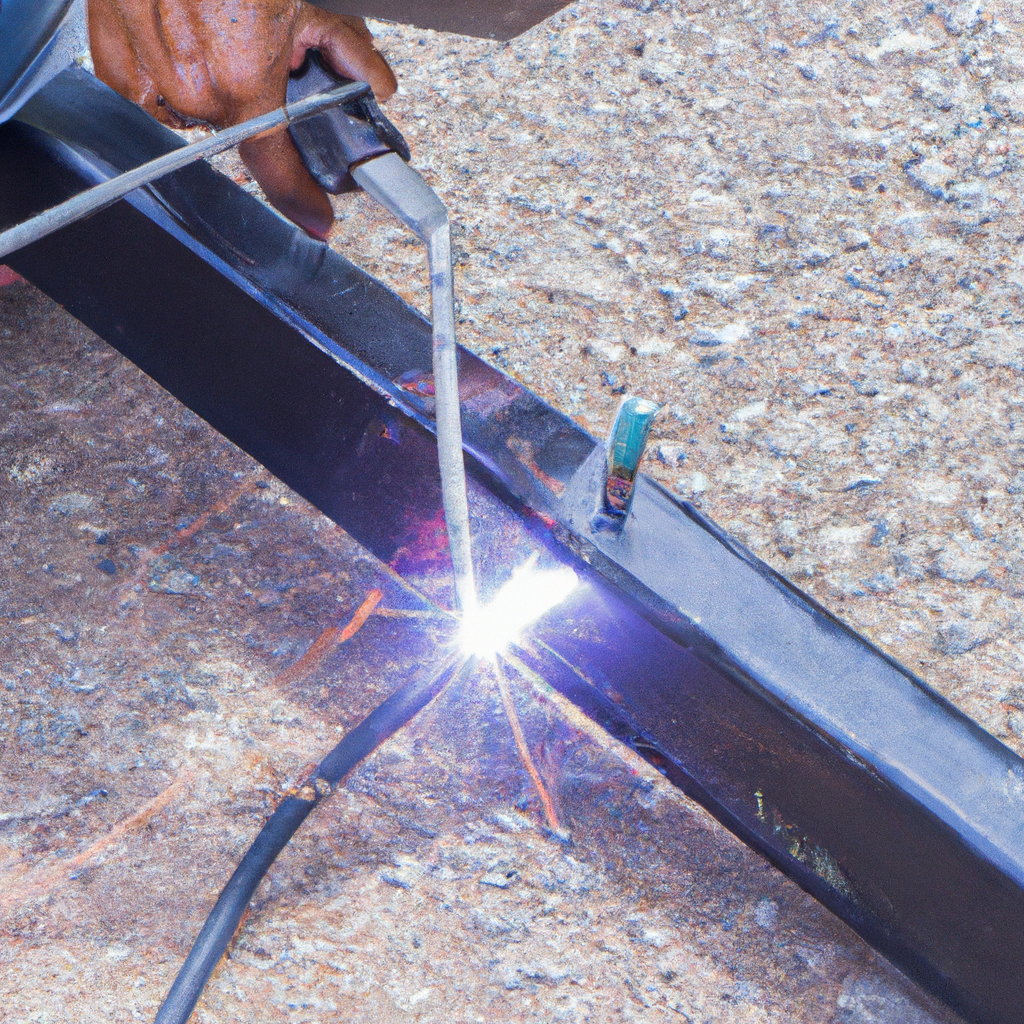
When welding high carbon steel, it is important to take safety precautions to ensure the safety of the welder and those in the vicinity.
First, it is important to wear the appropriate safety gear, including a welding helmet, gloves, and protective clothing. The welding helmet should be equipped with a filter lens that is suitable for the type of welding being performed. Additionally, it is important to wear a respirator to protect against fumes and gases that may be released during the welding process.
Second, it is important to ensure that the welding area is well-ventilated. This will help to reduce the risk of exposure to hazardous fumes and gases. Additionally, it is important to keep combustible materials away from the welding area.
Third, it is important to use the correct welding technique for the type of steel being welded. High carbon steel requires a higher welding temperature than other types of steel, and it is important to use the correct welding rod and technique to ensure a successful weld.
Finally, it is important to inspect the welded joint for any defects or cracks. If any defects are found, it is important to repair them before continuing with the welding process.
By following these safety precautions, welders can ensure that they are welding high carbon steel safely and effectively.
What Are the Different Techniques for Welding High Carbon Steel?
Welding high carbon steel requires special techniques to ensure a strong, reliable weld. The following techniques are commonly used when welding high carbon steel:
1. Shielded Metal Arc Welding (SMAW): SMAW is a manual welding process that uses a consumable electrode covered with flux to lay the weld. This process is often used for welding high carbon steel components that require high strength and good weldability.
2. Gas Metal Arc Welding (GMAW): GMAW is a semi-automatic welding process that uses a consumable wire electrode and an inert gas to protect the weld from contamination. This process is often used for welding high carbon steel components that require high strength and good weldability.
3. Flux-Cored Arc Welding (FCAW): FCAW is a semi-automatic welding process that uses a consumable wire electrode and a flux-cored wire to lay the weld. This process is often used for welding high carbon steel components that require high strength and good weldability.
4. Submerged Arc Welding (SAW): SAW is an automated welding process that uses a consumable wire electrode and a flux-covered electrode to lay the weld. This process is often used for welding high carbon steel components that require high strength and good weldability.
5. Gas Tungsten Arc Welding (GTAW): GTAW is a manual welding process that uses a non-consumable tungsten electrode and an inert gas to protect the weld from contamination. This process is often used for welding high carbon steel components that require high strength and good weldability.
What Are the Best Practices for Welding High Carbon Steel?
Welding high carbon steel requires a few extra steps to ensure a successful weld. The following best practices should be followed when welding high carbon steel:
1. Preheat the steel: Preheating the steel before welding helps to reduce the risk of cracking and warping. Preheating should be done slowly and evenly, and the temperature should be monitored with a thermometer.
2. Use the right filler metal: The filler metal should match the base metal in terms of carbon content. This will ensure that the weld is strong and will not crack.
3. Use the right welding technique: High carbon steel should be welded with a low-hydrogen process such as shielded metal arc welding (SMAW) or flux-cored arc welding (FCAW).
4. Use the right shielding gas: Shielding gases such as argon or helium should be used to protect the weld from oxidation.
5. Use the right welding parameters: The welding parameters should be adjusted to ensure that the weld is strong and free of defects. The amperage, voltage, and travel speed should all be adjusted to the correct levels.
6. Post-weld heat treatment: Post-weld heat treatment is recommended for high carbon steel welds. This will help to reduce the risk of cracking and warping.
Following these best practices will help to ensure a successful weld when welding high carbon steel.
What Are the Common Challenges of Welding High Carbon Steel?
Welding high carbon steel presents several challenges to welders. The high carbon content makes the metal more prone to cracking, warping, and distortion during the welding process. Additionally, high carbon steel has a higher melting point than other steels, making it more difficult to weld. The high carbon content also makes it more difficult to achieve a uniform weld bead.
To address these challenges, welders must use the correct welding technique and equipment. Preheating the metal before welding is essential to reduce the risk of cracking and warping. Additionally, using a low amperage and a slow welding speed can help to reduce the risk of distortion. Finally, using a filler metal with a lower carbon content than the base metal can help to achieve a uniform weld bead.
What Are the Different Types of Welding Rods for High Carbon Steel?
High carbon steel is a type of steel that contains a higher amount of carbon than other types of steel. It is often used in the construction of tools and machinery, and is known for its strength and durability. Welding high carbon steel requires the use of specific welding rods that are designed to handle the higher carbon content.
The most common types of welding rods for high carbon steel are low hydrogen rods, such as E7018 and E7016. These rods are designed to reduce the amount of hydrogen in the weld, which can cause cracking and other issues. They are also designed to provide a strong, reliable weld.
Another type of welding rod for high carbon steel is the nickel-based rod, such as ENi-Cl. These rods are designed to provide a strong, reliable weld that is resistant to corrosion. They are also designed to provide a higher level of ductility, which makes them ideal for welding high carbon steel.
Finally, stainless steel welding rods, such as E308L and E316L, are also suitable for welding high carbon steel. These rods are designed to provide a strong, reliable weld that is resistant to corrosion and oxidation. They are also designed to provide a higher level of ductility, which makes them ideal for welding high carbon steel.
Conclusion
Welding high carbon steel requires a great deal of skill and knowledge. It is important to use the right welding technique, the right welding rod, and the right welding machine. It is also important to use the right shielding gas and to preheat the steel before welding. With the right preparation and technique, high carbon steel can be welded successfully and with good results.