Steel and steel alloy elements are defined as:
It is an iron-carbon alloy called steel. Small amounts of silicon, manganese, sulfur, and phosphorus are included in this alloy.
These sums are typically:
from 0.1 to 1.7 (rarely 2%) Carbon (C) (C)
0.15 – 0.40% Silicon (SI) (SI)
0.40% – 0.80% Manganese (Mn) (Mn)
Sulfur, 0.030% to 0.060% (S)
Phosphorus (P) ranges from 0.030 to 0.050% and is present in all steels.
The phrase “alloy steel” is often used to denote the presence of alloying components other than carbon in the composition of steel, even though steel is an alloy of carbon and iron. In actuality, carbon serves as an alloying in the steel structure and is the most significant one, along with other alloying elements. Although it is untrue, carbon is often seen as being beyond the purview of alloying elements. Steels are often split into two primary categories as CARBON STEELS and ALLOY STEELS based on this historical division.
CARBON STEELS and ALLOY STEELS
All carbon steels could include substances like Cr, Mo, Cu, Ni, etc. that are naturally occurring during the manufacture of the steel but aren’t purposefully added for alloying reasons.
An element that is purposefully added to steel in order to enhance a certain quality is known as an alloying element. For instance, chromium is an alloying element when it is added to enhance rust resistance, while tungsten is an alloying element when it is used to improve wear resistance.
Sulfur and phosphorus, in the traditional sense, are the components that adversely impact the intended steel qualities in the structure of the steel yet unavoidably and randomly enter the steel during steel manufacturing.
Sulfur and phosphorus, however, should be classed as an alloying element if they are introduced to the steel composition for a particular purpose, as in certain high sulfur and high phosphorus readily machinable (automated) steels.
If we list the impacts of the components of steel’s composition on steel;
-
Carbon:
(C) The most fundamental alloying component of steel is carbon. It is the most crucial component in making steel stronger and harder. The tensile strength and yield strength of the steel improve as the percentage of perlite and the percentage of C both rise. On the other hand, when C% rises, the steel’s ductility and weldability diminish, and its propensity to break after quenching rises. Compared to certain other elements, like phosphorus, carbon is often less prone to buildup. However, the mechanical characteristics of the steel are significantly impacted because carbon buildup (segregation) deteriorates the homogeneity of the steel in its structure. The most noticeable aspect of carbon buildup is sequencing (banding).
Steel’s strength is increased by manganese (Mn). It marginally lessens the ductility. By causing hardening in the ferrite solid solution, manganese boosts the steel’s strength. Manganese has a favorable impact on the steel’s malleability and hardenability, but not so much on weldability. Manganese has a growing impact on surface quality in steel at all carbon ratios. The element with the lowest propensity for coarse buildup is manganese. One of the fundamental materials utilized to eliminate oxygen during the manufacturing of steel is silicon (Si). They have up to 75% Si content. For electrical purposes, these are specific steels. Good alloy steel with 14–15% silicon content has very high corrosion resistance, however silicon has a smaller impact than manganese. Additionally, the resistance rises. Low carbon steels’ surfaces are negatively impacted by silicon; this negative impact is particularly noticeable in sulfur steels that are simple to machine.
-
Sulfur:
(S) Except for sulfur steels that are simple to machine, sulfur is not a desirable component in steel compositions. In the steel composition, it should be maintained as low as feasible. Transverse ductility and notched impact toughness values decrease with decreasing sulfur concentration, although they have little effect on longitudinal characteristics. when manganese and sulfur are in equilibrium Hot brittleness is the result. It often appears as sulfur and oxysulfide residues in steel structures and has a strong propensity to accumulate. Particularly in low carbon and low manganese steels, it impairs surface quality. The weldability feature is drastically diminished. Sulfur is thus seen as a detrimental addition and has a propensity to build in the makeup of steels. limited to %.
The ingredient that gives ferrite the greatest boost in strength is phosphorus (P). Therefore, even in little amounts, phosphorus makes steel stronger and harder while decreasing ductility and notch toughness in the rolling direction. These adverse consequences are particularly pronounced in high carbon tempered steels. less prone to buildup than sulfur and carbon. Steel’s resistance to corrosion is enhanced by phosphorus. Particularly when the steel is discovered in modest quantities with copper in its structure, this beneficial impact rises.
-
Chrome (Cr) :
It is included into the steel’s formula to improve hardenability, corrosion resistance, and oxidation resistance. It serves as the fundamental component of stainless steel alloys. Since chromium is a carbide-forming element, it is utilized to strengthen the friction resistance of steels used in high temperature applications as well as the wear resistance of tool steels with high carbon content.
-
Nickel:
(Ni) Steel becomes stronger because to nickel’s ability to harden solid solutions in ferrite. To make the real steel more resilient, nickel is added. After chromium, nickel is the most significant alloying component found in stainless steel compositions. They also serve as the primary alloying component in heat-resistant steels, which improves the steel’s resistance to oxidation. Nickel is added to steeling that contains copper to avoid or lessen the hot embrittlement that copper causes.
-
Molybdenum :
(Mo) is a metal that is present in low alloy steels at a rate of 15–0.30% and typically performs best when combined with chromium and nickel. Steels are more able to be hardened and are stronger thanks to molybdenum. The reduction of temper brittleness is one of molybdenum’s most significant impacts.
-
Vanadium:
(V) It enhances the hardenability to some amount, comparable to other alloying elements. Tool steels are enhanced with vanadium, one of the strongest carbide formers, to raise the hot hardness value. In high speed steels, it is combined with tungsten, while in structural and heat resistant steels, it is combined with chromium.
-
Tungsten:
Tungsten makes steel more durable. The primary benefit is that it produces secondary hardening in high speed steels, which gives hot hardness.
-
Niobium:
It improves the steel’s tensile and yield strengths to a certain degree.
-
Titan:
It is added to the composition as a stabilizer against sensitization, particularly in austenitic stainless steels. In common applications, titanium is often utilized to minimize the size of the grain. It is applied to steels stabilized with AL the most successfully since it is also a potent oxygen remover.
-
Zikron:
This substance is mostly used to manage residue. In particular, it improves toughness by altering the sulfur residues’ physical shapes.
-
Cobalt:
Due to its ability to suppress grain development at high temperatures, it is mostly added to high speed steels and hot work steels. Because of its magnetism, cobalt has a favorable impact on heat conductivity as well.
-
Aluminum:
(AL) The strongest deoxidizer is it. It lessens the sensitivity to strain-aging because it produces nitrides when combined with nitrogen. In the manufacture of steel, aluminum is also employed as a grain reducer.
The ingredient that most efficiently increases the hardenability of low- and medium-carbon steels is boron (B).
-
Copper:
(Cu) It lessens the steel’s flexibility while enhancing its strength and hardness. The fact that it makes steels more resistant to atmospheric regeneration is its most significant feature. Low amounts of copper do not impair the steel’s weldability, but they do produce hot brittleness, which has a similar effect to sulfur in hot forming steels.
-
Lead:
(Pb) It is only added to the composition of readily machinable free-cut steels with lead since it is not soluble in steel.
-
Selen:
When simple machinability is needed, it is added to the composition of steels, particularly stainless steels. Steel’s resistivity is decreased less than that of other comparable elements.
-
Oxygen:
(O) Rather than in its pure condition, oxygen generates hazard via the oxide residues it leaves behind.
-
Nitrogen:
This element is crucial since it produces nitrides. To boost the hardness and yield strength at high temperatures and to improve the composition of stainless steels, it is particularly added.
The most hazardous component of a steel construction is hydrogen. It penetrates the steel by the use of damp raw materials and additives as well as hydrocarbon origin. It takes a while and is hard to get rid of.
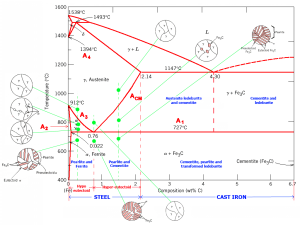
At a carbon content of 4.3%, the molten iron-carbon alloy takes on a “ledebunite” texture. Iron-graphite is created when alloys with more than 2.06% carbon and a little amount of silicon in the C point are cemented after being cooled down extremely slowly.
Solidification as a combination of iron cementite and carbide Here, a little quantity of carbon breaks down into tiny particles of perlite while a huge amount of carbon transforms into particles of graphite. Thus, pure perlite zones that are rounded into ferrite+perlite or graphite plates are created when high carbon content iron materials transition from a molten state to a solid one. shows that the surplus carbon in the cast iron has produced graphite plates.
The image shows the variations in texture that take place when carbon steels get harder. The carbon content of the steel and the level of tempering both affect how the texture forms and changes. In the diagram, the abscess (x-axis) represents the carbon ratio. Here, ferrite (pure iron) with a carbon content of 0%, pure perlite with a carbon content of 0.8%, cast iron with a carbon content of 2.0%, low-melting iron with a carbon content of 4.3%, and cementite alloy with a carbon content of 6.67% are all indicated. In the following carbon ratios, alloying is not possible. The final ratio is 6.67%.
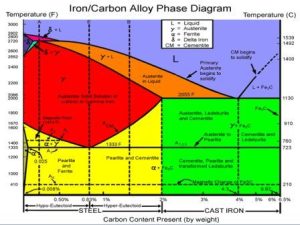
Austenite , Perlite, Ferrite
On A3-ACM, Austenite may be found. It is non-magnetic and gentle.
Perlite: The 0.89 C eutectoid steel structure is made of cementite and ferrite and is known as perlite.
Ferrite: This is a trace quantity of C-prayer iron. It’s incredibly delicate.
Martensite: This rigid, needle-like structure is created when austenite cools suddenly.
Baynit: The process of cooling austenitized steel on MS.
In a shell made of austenitized steel, sorbit.
Nitriding is the process of drying a nitrogen-containing atmosphere, such as ammonia, at a temperature of 490-520 C in appropriate steels.
ACM: This is the temperature at which supra-eutectoid steels are heated to the point at which cementite and austenite completely convert into austenite.
The temperature at which a solid metal tissue phase occurs is known as the transformation temperature.